10 Questions With… Brian Peters
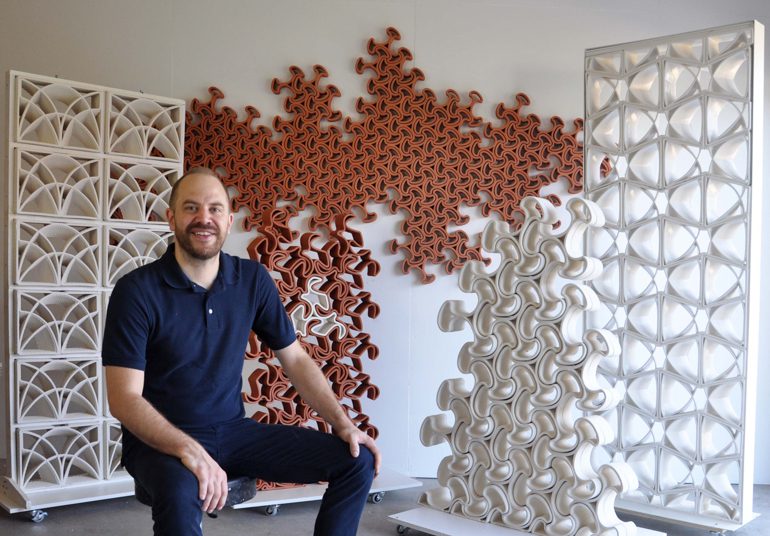
Trained as an architect and artist, Brian Peters has melded the two into a distinctive career intersecting both worlds. His medium is 3D-printed ceramics. Thus, fabrication enters the mix. As does the junction between the high-tech digital realm and the traditional, artisanal techniques of kiln drying and glazing that are part of the process. His works run the gamut from freestanding screens and wall-mounted pieces to large-scale installations commissioned by such public institutions as the state of New Jersey, the Olbrich Botanical Gardens in Madison, Wisconsin, and the Carnegie Museum of Art. Architects are clients, too, among them Bohlin Cywinski Jackson. Everything is created in Peters’ studio in Carnegie, Pennsylvania, outside of Pittsburgh, as is the residence he shares with his wife Daphne, an assistant teaching professor at Carnegie Mellon School of Design, and children, Matthias, 6, and Zoe, 3. Peters, though, is a world citizen. He lived in Barcelona and Amsterdam, following seven years in Chicago and holds a bachelor of studio art degree from Calvin College (Grand Rapids), a master’s degree in architecture from the University of Illinois at Chicago, and a master’s degree in advanced architecture from the Institute for Advanced Architecture of Catalonia, Barcelona.

Interior Design: What in your background sparked interests in architecture and art?
Brian Peters: I grew up in Grand Rapids, Michigan, as the youngest of four children. My father taught high school history; my mother was a nurse. Art, architecture, and design weren’t of great interest to other members of my family, but a visit to Frank Lloyd Wright’s Meyer May house sparked mine. By high school, I realized that leaders of commercial furniture design such as Steelcase, Herman Miller, and Haworth were all in the Grand Rapids area.
ID: You had a travel-rich start to your career, starting in Barcelona. What drew you to that vibrant city?
BP: I was working as an architect in Chicago when I decided to return to school and immerse myself in the emerging fields of digital design and fabrication, such as 3D printing. At the time, one of the few places offering a degree in advanced architecture with a focus on what they called “digital tectonics” was the IACC. We were already familiar with the city. [Brian and Daphne met in Barcelona during a study abroad program]. After completing my second master’s, I stayed and taught at the university for another year.
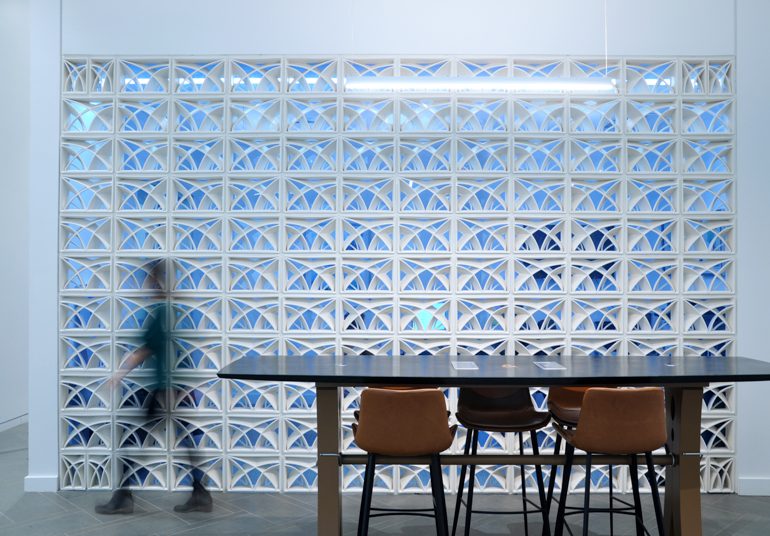
ID: Next up was Amsterdam. How did that come about?
BP: I was hired by DUS as an architect and asked to devise an idea for an interesting temporary pavilion. Having spent two years working with emerging technology, I pitched them the idea of creating a giant 3D printer, which could then 3D print small-scale pavilions. I was able to make the idea a reality by collaborating with such specialists as 3D printing experts, mechanical engineers, and material extrusion experts.
ID: What was the catalyst leading to 3D printing as your artistic medium?
BP: My exploration of 3D-printed ceramics started during a residency at a ceramic center in the Netherlands. I was working with bioplastics for the large-scale 3D printer with DUS, but I started to question the use of plastics at all. I was curious to see if I could hack existing 3D printers to use a more sustainable material like ceramics. This initial exploration led to the Building Bytes project, [a collection of 3D-printed ceramic bricks]. It was launched at Dutch Design Week 2012 in Eindhoven and exhibited around the world.
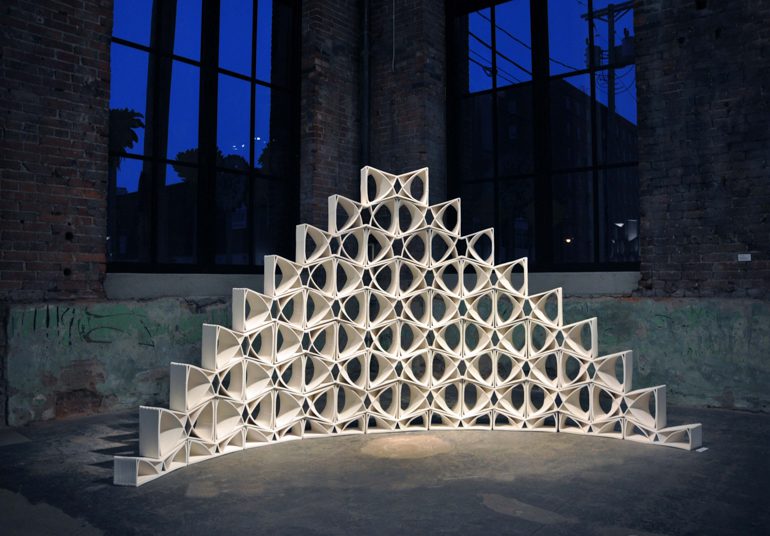
ID: How did the project evolve?
BP: Initially, Building Bytes was a speculative prototype. I spent the next four years scaling up the process, building larger custom 3D printers, testing various design options, and learning more about ceramics and glazing. Once I felt like I had a solid foundation, I began pursuing public art commissions. In 2017, I dedicated my practice solely to creating 3D-printed ceramic works for art installations.
ID: How does your process work?
BP: Once I develop a pattern and form, I translate two-dimensional sketches and drawings into digitally-modeled 3D geometries that will be materialized in space. The parametric design process allows me to explore scale, dimensionality, and the link between overall form and infills before I begin working with the physical material. I then 3D-print a small-scale prototype and use it to inform the next round of prototypes. Experimentation and prototyping are key aspects of my work. Final pieces then dry for several days. After the initial kiln firing, they are hand glazed following traditional artisanal methods and kiln fired again.
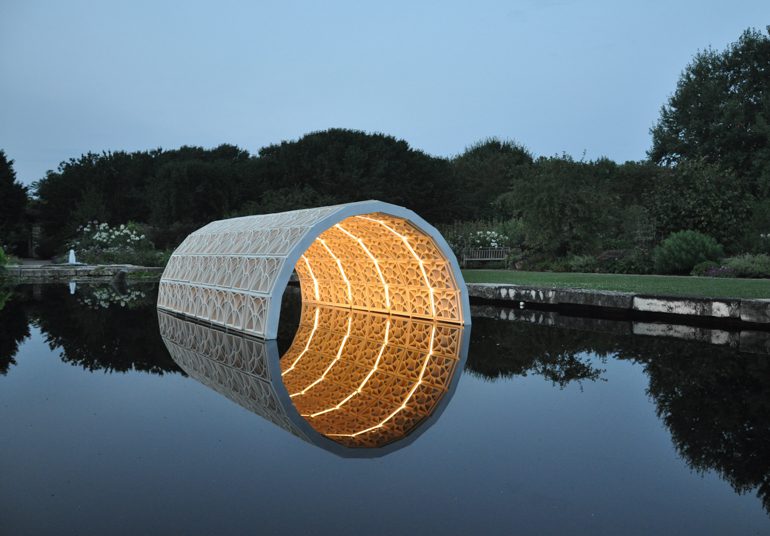
ID: How do most of your commissions come about?
BP: Some clients have sought me out with specific commissions in mind. Others have come through referrals. Bohlin Cywinski Jackson’s studio asked me to create wall-mounted ceramic installations for a technology’s new Pittsburgh office. It was the first commission from an architecture firm, and the collaboration with their team was a rich experience. Most of my public art projects were commissioned through the traditional proposal process.
I’m excited to be participating in the upcoming ICFF in November. It will be wonderful to get feedback directly from the design community. I look forward to potential projects that might come from it.
ID: Congratulations. You were a NYCxDESIGN finalist for your Polsky screen. Tell us about it.
BP: One of my first large-scale public art commissions, it was for an Akron, Ohio program that activates empty storefronts with temporary installations. I developed a block design inspired by the ornate terracotta façade of the historic Polsky building. The block’s unique bow-tie form allows them to be installed for both temporary and permanent projects. For the former, blocks are stacked and support each other without needing mortar or grout. For permanent placement, I work with professional tile installers.
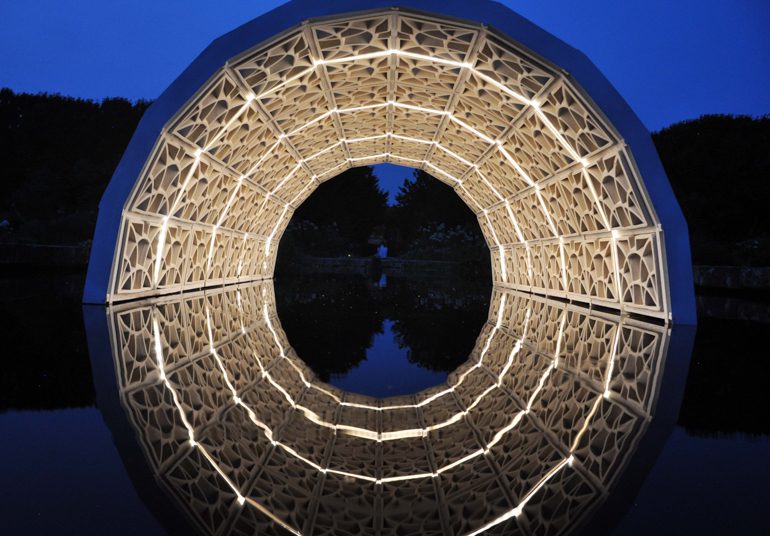
ID: From where do you draw inspiration?
BP: I am inspired by the intricacies of flora, the artistry of patterning, and the complex geometries of contemporary forms. There is great beauty in our surroundings, and I am often inspired while on strolls through urban areas or on hikes through state parks. For commissions, I look for projects’ unique contexts.
ID: What are you reading, watching, listening to?
BP: I’m currently reading books about running small businesses. I’m watching comedies because during these crazy times I need a good laugh. Music is always playing in my studio, from rock-a-billy to electronic sound, indie rock, and blues. It’s an eclectic mix.
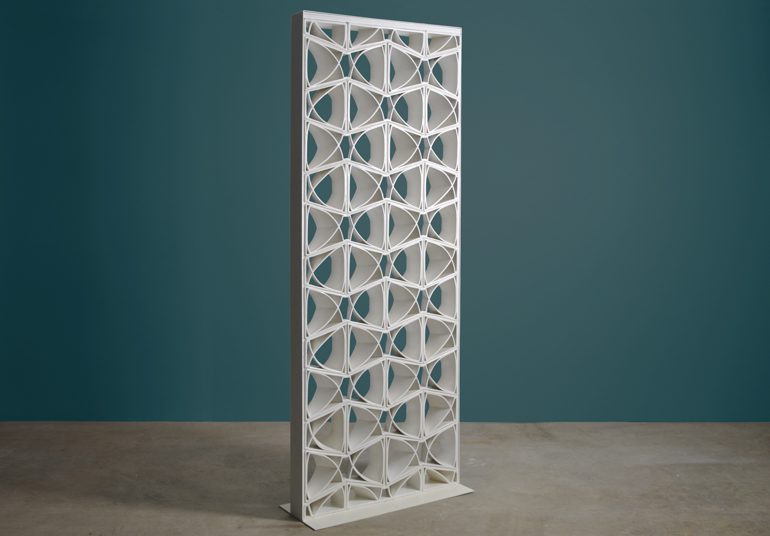

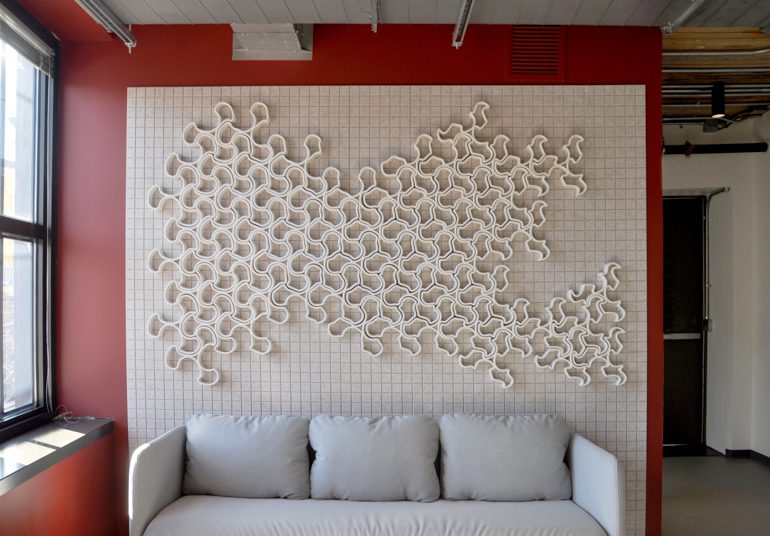