Q&A: Marc Fornes on Creating Intricate Sculptures With Code
Working on an experimental carbon-fiber shell for Zaha Hadid Architects in the early 2000’s, Marc Fornes became fascinated with materials research and geometric forms. He had already studied mathematics in addition to architecture, and he drew on that cumulative knowledge when he founded his own studio, Marc Fornes/TheVeryMany, in Brooklyn, New York. His 10-person team now applies computational protocols to ever bigger and more complex curvilinear structures.
They run the gamut from site-specific sculptures to pop-ups for Louis Vuitton and even private residences. His most recent projects include a public sculpture, made from 5,312 components, for the World Expo in Kazakhstan and the Chrysalis amphitheater at Merriweather Park in Symphony Woods in Columbia, Maryland. Here, Fornes discusses the art of turning data into design.
Interior Design: Where did you grow up?
Mark Fornes: I was born in Strasbourg, France, on the border with Germany. We speak French, but the food and wine are very German. There is something about being born on a border—I’m always trying to understand things from many sides.
ID: Is that why you call your studio TheVeryMany?
MF: The name comes from two simple things. First, you can understand anything in nature or the built world if you break it apart and study its many elements. Second, the design process depends on a team, not one single person. Everyone is important, from the designer to the coder to the fabricator. We write our code into a computational syntax, which is executed to generate geometry, its constituent parts, and fabrication files for digital manufacturing.

ID: Even though your work is based on mathematics, it feels inspired by nature.
MF: I like that people can see the sea or flowers or bones in our environments. But we are not intentionally doing biomimicry. We are not looking at coral and building a giant coral. No. It may seem like we are only because our double curved surfaces are similar to the geometry of nature.
ID: Similar in what way?
MF: Our surfaces have to curve in two different directions, which we describe as linear and nonlinear computational stripes. How can we build such a surface without molds or scaffolding? You lay the stripes on paper, one next to the other, to create a shell. You can have an endless number of unique single elements or what we call single stripes, with many more connected to neighbors.
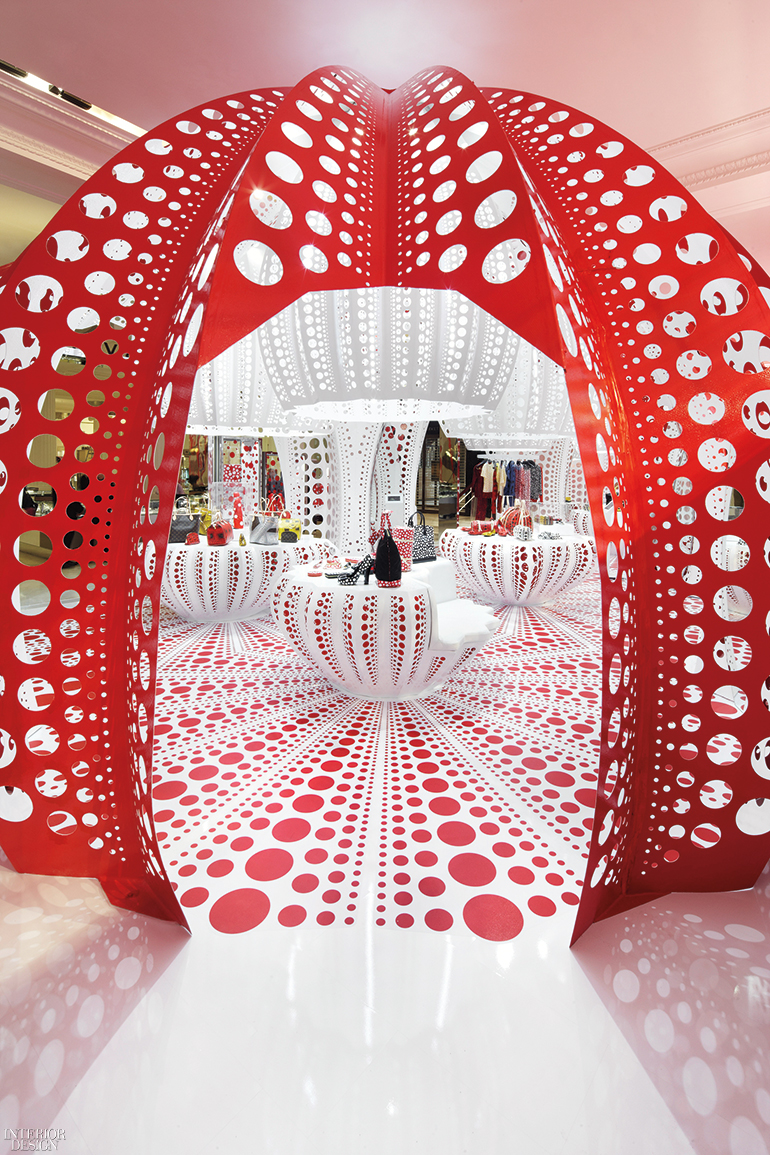
ID: Can a whole structure fail because of a code glitch?
MF: We do not rely on the pseudorandom generators used by, say, graphic designers. From the first time that you execute your code, you have to deal with any mistakes at the code level. We are always learning from failure on both the computational side and the physical side. We extract all kinds of statistics that we use as a premise for future projects.
ID: What do those stats tell you?
MF: Whether the structure is scalable to the next level. A protocol might work for a site-specific artistic installation but cannot reach the scale of architecture. We are always pushing to scale up.
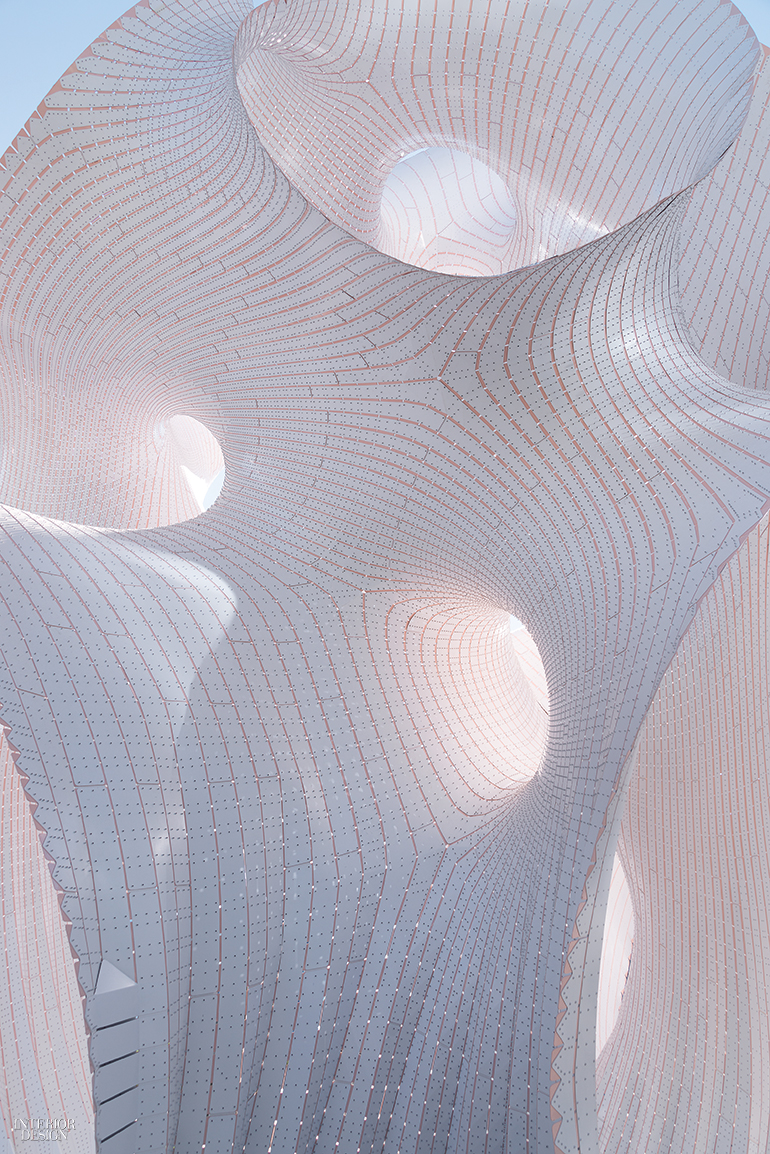
ID: Can you just tweak the algorithm to enlarge the result?
MF: Making assumptions on a laptop screen is very different from experiencing a 3D prototype. That’s where you discover unexpected qualities about acoustics and light effects.
ID: How much time do you spend testing a design?
MF: A lot. Recent projects always serve as a precedent. Plus, the process can involve two or three full-scale mock-ups. We’re looking at ways to fit parts together, the number of parts, how many sheets of metal, how many struts, the way that systems go up. These are steps you cannot bypass. The keystone between the computational research and the materials system is the logistical.
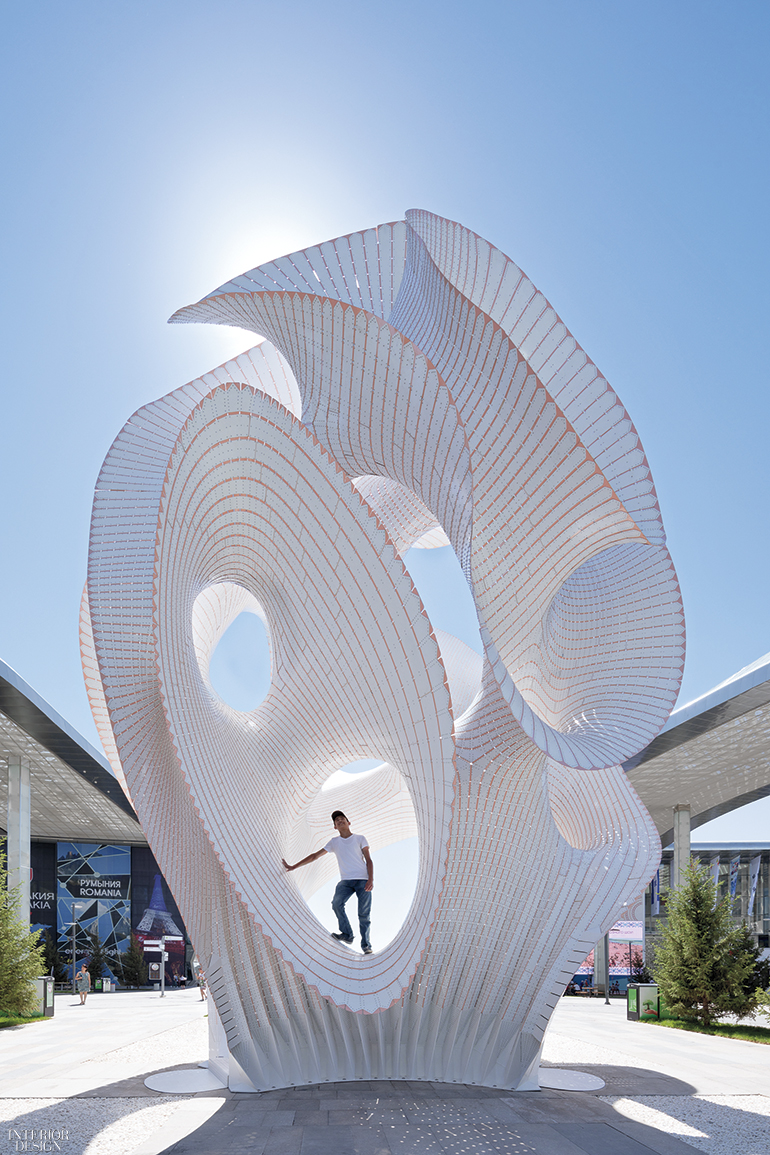
ID: How do you resolve the logistics?
MF: By understanding digital production. There’s a lot of back-and-forth, exploring the materials and how to process them for specific programs. Then we think about how we can reassemble those endless sets of parts. Can five parts become one? How can we arrive at that on the computational side?
We provide the fabricator with all the machining files. That’s different from conventional architecture, which often stops at shop drawings. For most of our installations, we use a specific machine we developed to fold aluminum.
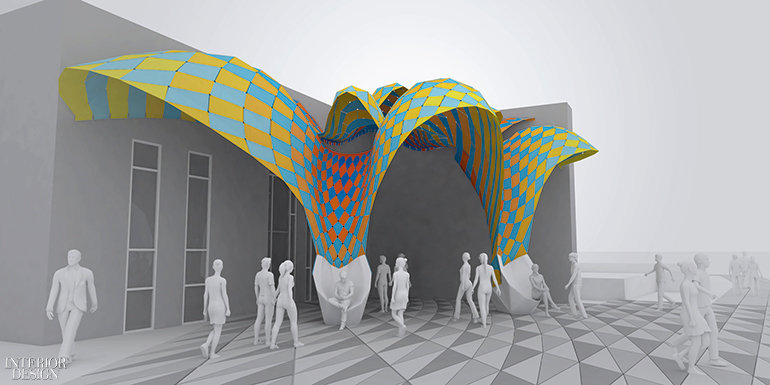
ID: What’s on the horizon?
MF: We have a project in Taiwan and another in Suzhou, China. In Florida, we’re doing a pier. In North Carolina, we’re doing the facade of an eight-story parking structure. For a public swimming pool in El Paso, we’re doing a canopy at the entry.
ID: Not the whole pool? To swim under one of your giant perforated canopies would be magical.
MF: Ah, yes. We would love to build that.
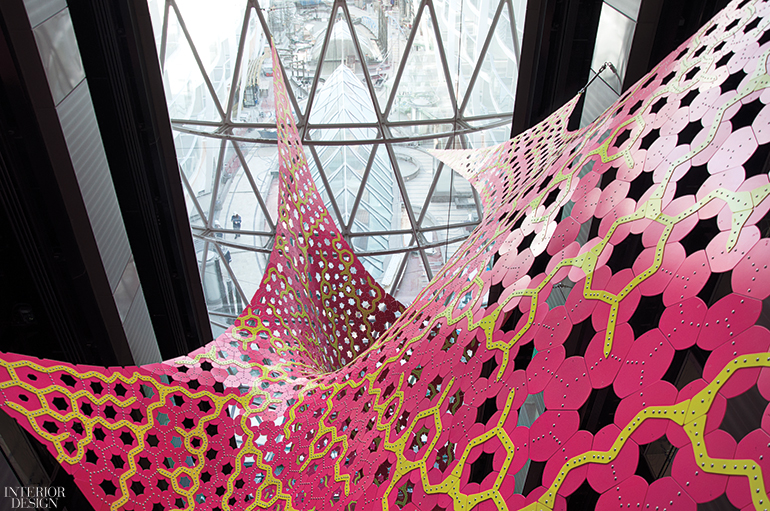
> See more from the October 2017 issue of Interior Design