Bates Masi + Architects Pays Tribute to an East Hampton House’s Modernist Predecessor
It’s nice living on the water. But when Superstorm Sandy hit Long Island in 2012, it destroyed a number of waterfront houses, including one midcentury dwelling on a lagoon in East Hampton, New York. When the owners decided to tear down the damaged structure and build a new residence, Bates Masi + Architects, based in the same town, proved a logical choice for the project. Firm founder and Interior Design Hall of Fame member Harry Bates has been designing modernist houses in the East End since the 1960s, when the original property was built.
The design needed to satisfy both memories and aspirations. The clients wanted it to be, as principal and fellow Hall of Famer Paul Masi eloquently puts it, “the child of the old one.” That meant it should reveal its structure honestly. “Our conversations kept returning to the fact that the design of the old house expressed how it was made,” he says. “There was a truthfulness to it that they really appreciated.” The new house would be on the exact same spot as the old one, with the same orientation, since the site had already been cleared and landscaped to accentuate the owners’ favorite vistas. But to comply with new flood zone requirements and avoid the same fate as its predecessor, the structure had to be built five feet above the ground.
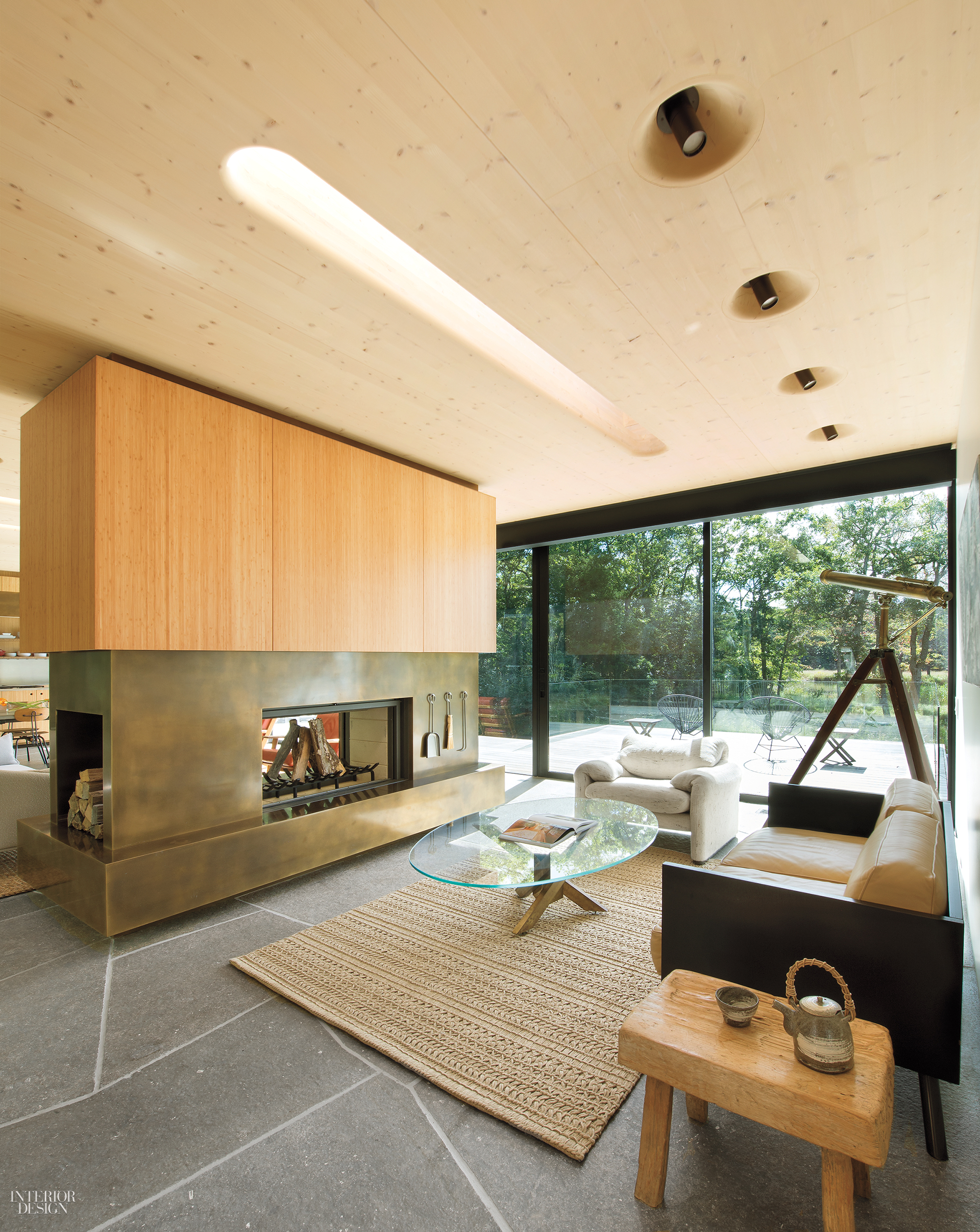
The 3,500-square-foot four-bedroom residence is slightly larger than the old one and sits on a concrete base, like a sculpture poised on a pedestal. In this manner, the glass-wrapped dwelling recalls Mies van der Rohe’s iconic Farnsworth House in Plano, Illinois—which is also raised five feet to avoid flooding. An open central volume containing the living/dining area and kitchen is flanked, nearly symmetrically, by bedroom wings. Exposed steel columns and beams support a roof made of cross-laminated timber, a product capable of spanning long distances—in this case, up to 30 feet. The CLT pine panels, like most of the house’s components, were readied for installation in a factory. That left much less to do on-site. “The contractor poured the slab, assembled the steel structure, craned the ceiling panels into place, and put up the doors and windows—and we were done,” Masi reports. “We didn’t so much as drill a hole.”
The firm is renowned for coaxing beauty and variety from a limited materials palette. “Too many ingredients spoil the stew,” Bates says. All paneling, indoors and out, is cypress. Cabinetry throughout is bamboo plywood, its exposed edges part of the “how it was made” motif. And anywhere stone was specified, the design team used the same fossil-flecked Montana limestone: outside, as sawn-finish rectangles that form steps and terraces leading from driveway to entry; inside, as irregular flamed slabs fitted together like a jigsaw puzzle to create the floor, their freeform edges a gentle counterpoint to all the right angles. Bathroom countertops are also made of the same stone, this time with a honed finish.
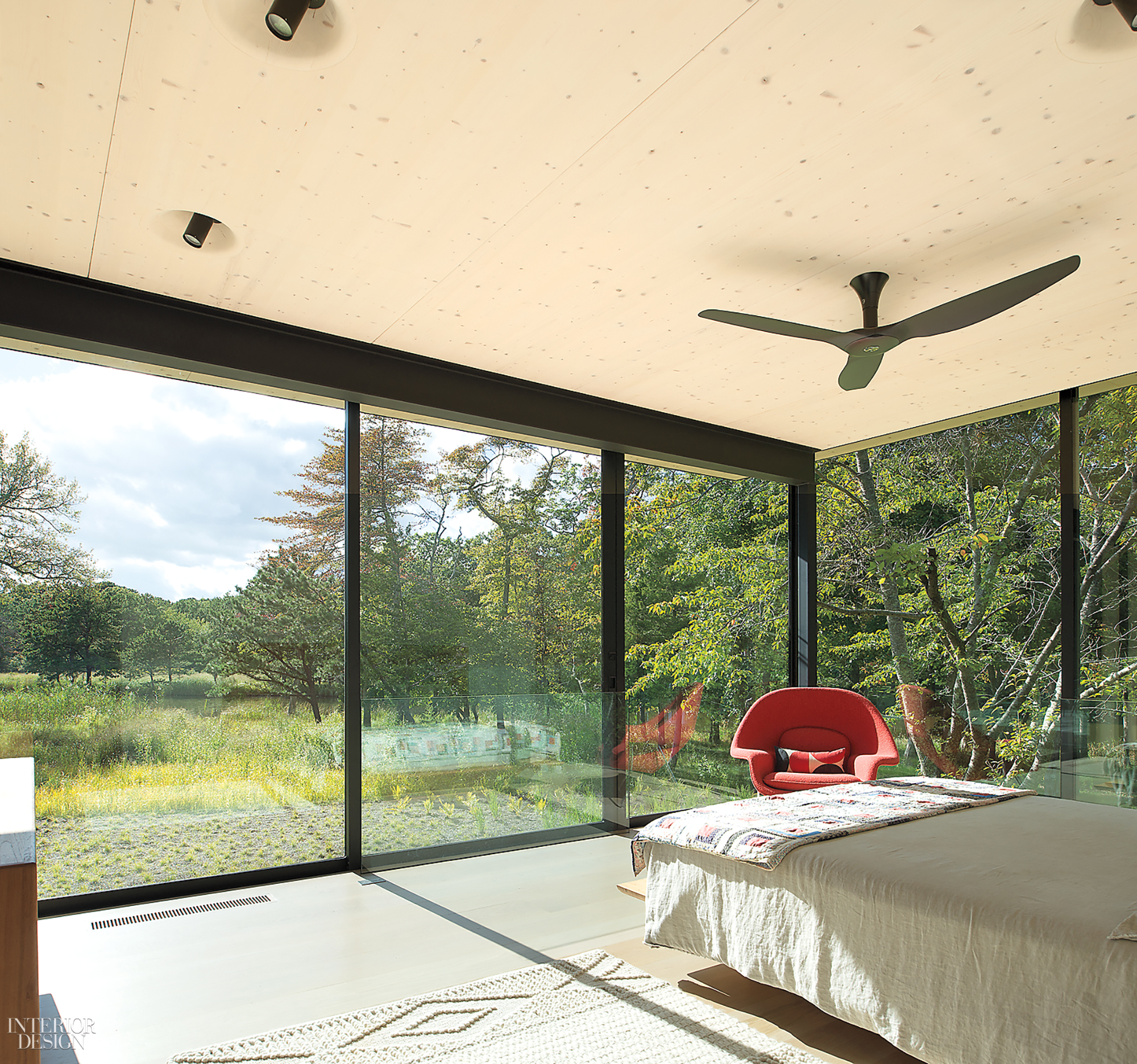
But the CLT perhaps proved most amenable to Bates Masi’s just-a-few-ingredients approach. Exposed on their underside to form the ceiling, the prefab pine panels accommodate lighting in rows of milled recesses, while elliptical perforations create skylights above the kitchen and living areas. The openings have radi-used lips, the precise curvature mocked up via 3-D printer. “The curves really showcase the laminated timber layers,” says Masi. “They’re also better for light distribution—you don’t get the hard shadows typical of overheads.”
Layered wood carved into sinuous forms is another recurring motif. Even the powder room sink was sculpted from a thick block of laminated bamboo plywood. Above it, a shallow recess in the cypress slats frames a lozenge-shape mirror.
Bronze door handles, rescued from the old house, inspired the choice of metal that surrounds the double-sided fireplace, which separates the living/dining area from a more intimate seating zone. The same material was wedded to a slice of CLT to create the custom chandelier illuminating the dining table—high-tech and yet gentle, like the house itself.
For all its architectural efficiency, the house is comfortable to live in. The abundant wood finishes and limestone floors lend warmth and texture. The owners brought in furniture from previous residences, including vintage armchairs in the living room and a bluestone dining table patinated from years of use. “Familiar pieces like that make the house feel like a home,” says Masi. How much the architects accomplished with a simple palette is a testament to their creativity. To return to Bates’s metaphor, you only need a few ingredients if you choose those ingredients wisely.
Project Team: Laguardia Design Group: Landscape Design. Steven Maresca: Structural Engineer. Peragine Millwork: Woodwork. Lettieri Construction: General Contractor.