Surf, Sand, and Concrete: Inside One Manufacturer’s Key to Success
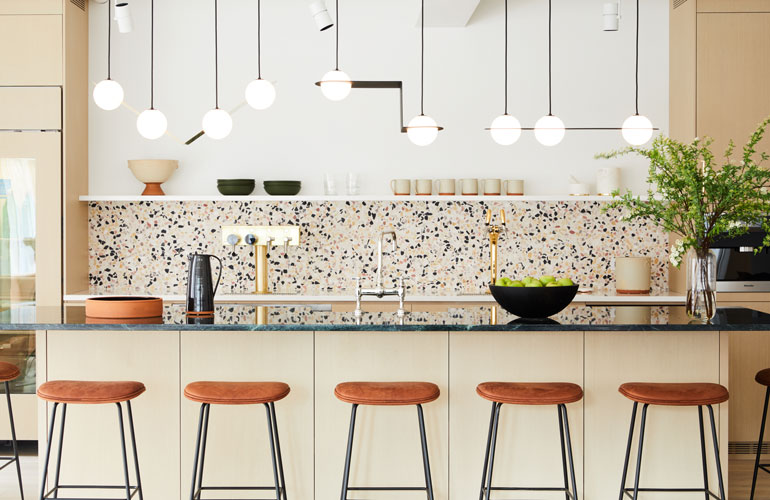
It’s hard to imagine New York City, known for its grit and shades of gray, without layers of concrete. The multi-faceted material, used widely since ancient times, permeates every corner, surface, and sidewalk throughout the five boroughs. Naturally, a company fueled by the creation of artisanal concrete and terrazzo surfaces—Concrete Collaborative—got its start in a Brooklyn garage more than 10 years ago, around the time industrial design was gaining mainstream appeal.
But Concrete Collaborative’s founders—sisters Kate Balsis, Hailey Weller, and Sally Smithwick, who grew up in Australia, and their spouses—never felt quite at home in New York’s densely populated urban landscape. The sisters longed for Australia’s sun and surf, leading them to venture west and relocate their families, and the family business, to a beach town reminiscent of home near San Diego. Since then, the innovative company, founded in 2007, has grown from a five-person operation to a team of nearly 60 people with a factory in California, and a flagship store in New York.
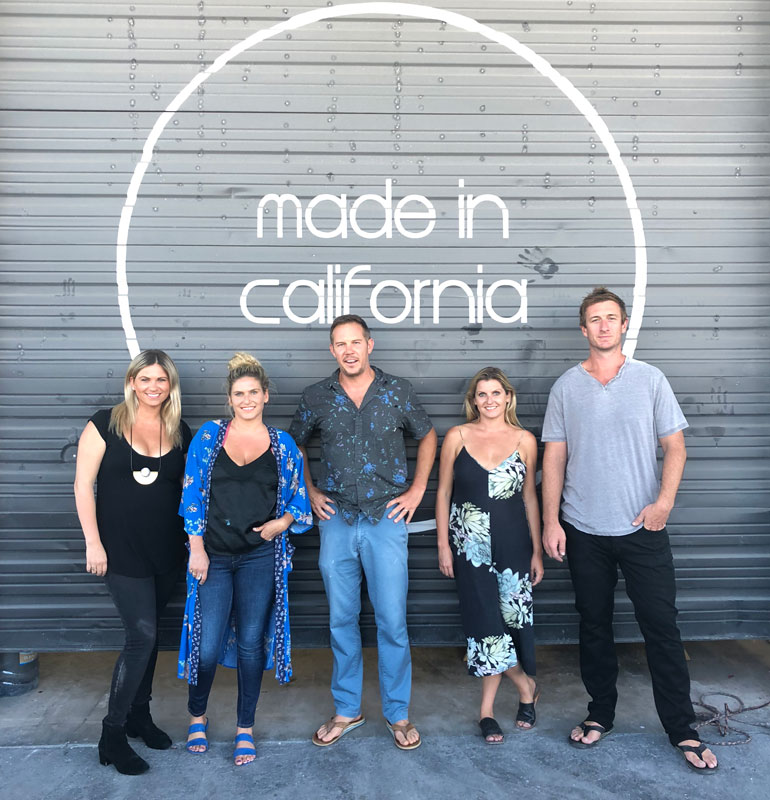
“My Dad was a civil engineer, who always worked with concrete, so his passion for the material inspired me to work with it,” says Balsis. “We started off with retail clients, which was our gateway into the market, and expanded from there.” And that first retail partner—Calvin Klein—marked Concrete Collaborative’s debut as a sought-after manufacturer of hand-crafted tiles, pavers, walling, slabs, stairs, and bespoke furniture. “We were cutting our teeth on one of harder segments of the industry, since retail schedules are quick and New York construction can be rough and tumble,” Balsis adds. “But that made us a pretty adept supplier.”
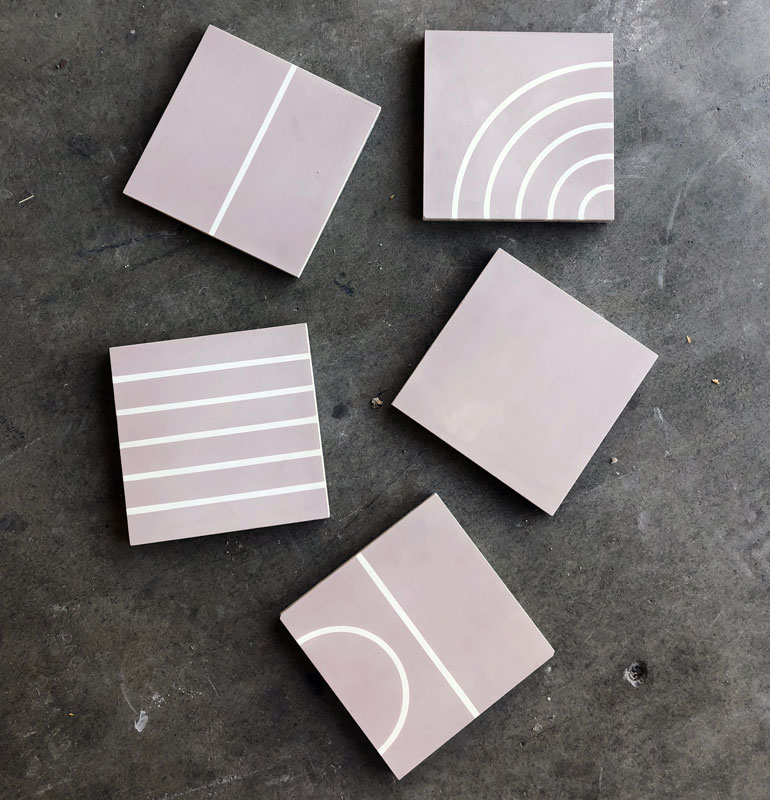
The company, which often names its products after beaches around the globe, innovates its portfolio by seeking out collaborations and partnerships that continuously push its designs forward. That’s exactly how Concrete Collaborative’s lauded SSS tile collection, a finalist for Interior Design’s 2019 Best of Year awards, came into existence. “If I like someone’s style, I reach out and ask if they’re open to working together on a collection; that’s exactly what I did with Sarah [Sherman Samuel] for the SSS collection,” explains Balsis. “We were asked to make commercial grade cement tile, and though there are a lot on the market from Morocco and Mexico, our processes are more advanced, so we could integrate different patterns.”
Samuel, a designer and lifestyle blogger, developed the five meditative patterns in Concrete Collaborative’s SSS tile collection, which launched at ICFF in New York earlier this year. Variations of crisp lines and soothing curves distinguish one tile from the next, inviting designers to play with shape, texture, and color in interior and exterior applications.
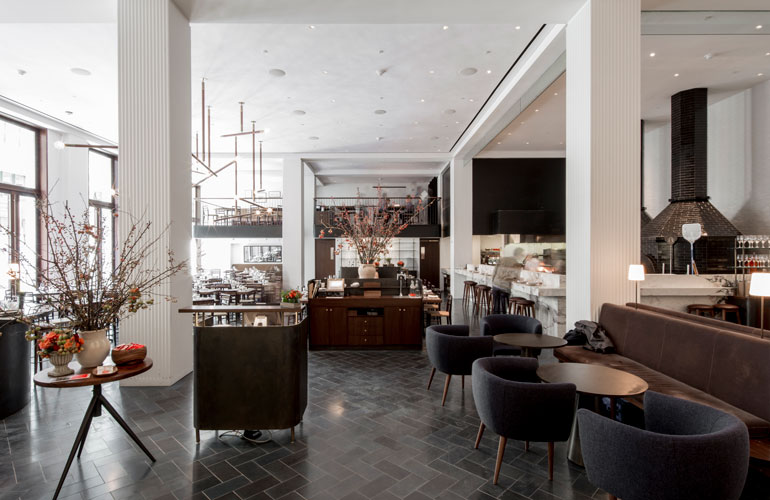
Though Concrete Collaborative makes working with concrete look easy, it’s a notoriously fickle material. “Synthetic products are much easier to control,” says Balsis. “Concrete is sort of like wood in a sense because there are so many natural variables occurring; it’s not easy to work with—it’s a bit of an art, and a bit of a science.” And knowing precisely how to reach that balance is how the company managed to disrupt the market for concrete and terrazzo surfaces with premium, hand-crafted products made in small batches.
Sustainable practices also are top of mind. All of the company’s products are made from responsibly sourced raw materials, such as premium cement, refined sand, and natural stone aggregates, which are then combined into a high density mix engineered for superior performance. Concrete Collaborative’s factory also uses a closed loop system to re-capture water, recycle concrete waste, and air cure products to eliminate carbon emissions that result from baking or firing.
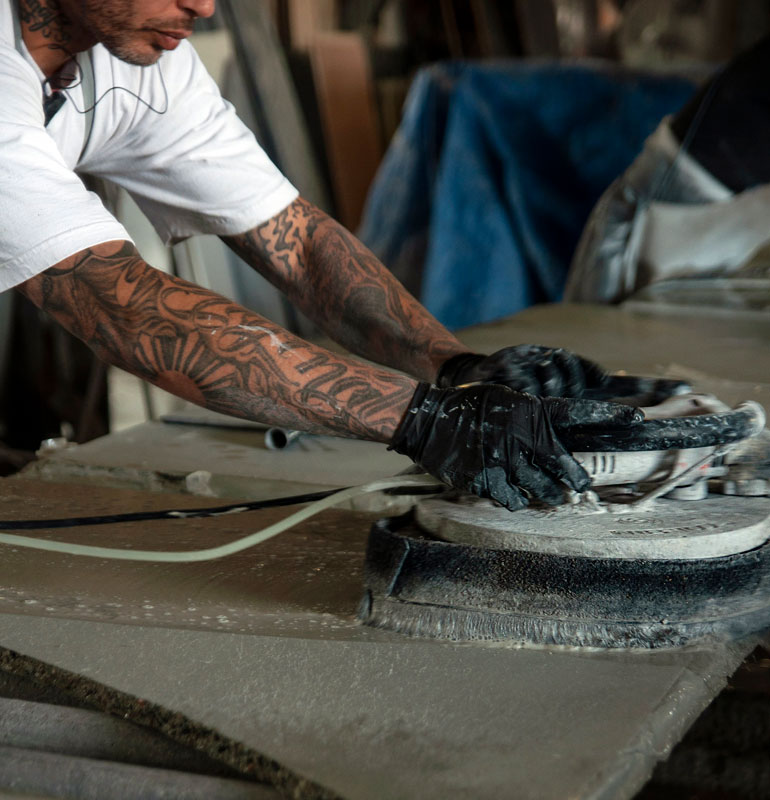
“Our sweet spot is being nimble enough to customize a color, for example, but being big enough and commercially-savvy enough to do large-scale projects under a tight timeframe,” says Balsis. “We’re constantly striving to innovate.”