4 Questions with… Industrial Designer John Reeves
For award-winning English designer John Reeves, sourcing local materials to create sustainable furnishings is top of mind. As is ensuring each piece evokes a sense of emotion, leaving a lasting impression on the user—and a given space. Reeves’s latest collection for Henry Hall Designs does exactly that, combining the fluidity of nature with the power of recycled aluminium to create a timeless 19-piece collection of indoor/outdoor furnishings.
The Flow collection, made of 100% recycled aluminium and FSC certified teak wood, exemplifies Reeves’s design philosophy—and that of Henry Hall Designs—in its variety of artfully crafted tables, chairs, benches, sofas, and chaise lounges. With graceful lines reminiscent of smooth river stones, and a durable zinc plate patina finish, the collection elevates sophisticated city rooftops and seaside home patios alike, adding to Henry Hall Designs expansive offerings. The Flow collection reflects the San Francisco-based brand’s ability to continuously innovate furniture design while working with renowned designers across the globe, like Reeves.
Here, Reeves shares with Interior Design his inspiration for the collection, the beauty of pieces that improve with age, and how he achieves silhouettes of lightness working with heavy, durable materials.
Interior Design: What elements most informed your design decisions when creating the Flow collection?
John Reeves: The Flow collection initially derived from wanting to explore the materiality of the metal casting process in sand. I loved the idea of being able to use a very archaic technique in sand casting, however I wanted to try and keep the integrity of the sand texture in the cast piece itself. This then lent itself to a more hardy and robust product with a nice stonelike texture that was not too cool to the touch—rather like a washed river pebble. The flowing lines that gave rise to the various forms came from a desire to try and capture that poured liquid state as a solid, almost like a drip in mid flow. This also benefited the processing as the tapered shape allowed for the metal to be lifted from the sand moulds without undercutting and crumbling the sand, like pouring jelly moulds.
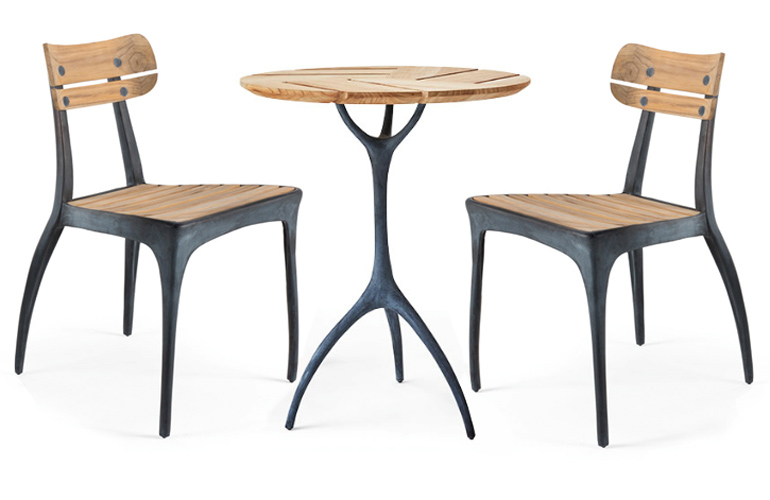
ID: Can you share more about the choice to use recycled aluminium. What are the benefits of using this material?
JR: Wherever possible, I am drawn towards utilizing sustainable or recycled materials in my designs. As this collection was going to be made using sand casting, which is essentially a gravity pour technique, it required a substantial amount of material to ensure strength and durability and avoid brittleness. It was clear that aluminium scrap as a raw material is available en mass if you know where to look for it, and with a little research I was able to find scrap yards that were separating good quality aluminium from various scooter engines, gas conduit pipes… As aluminium is such a malleable and ductile metal, the casting process and then the welding of components was super convenient in joining together seamless frames. In this instance it was almost alchemy—there was no need to pursue virgin aluminium.
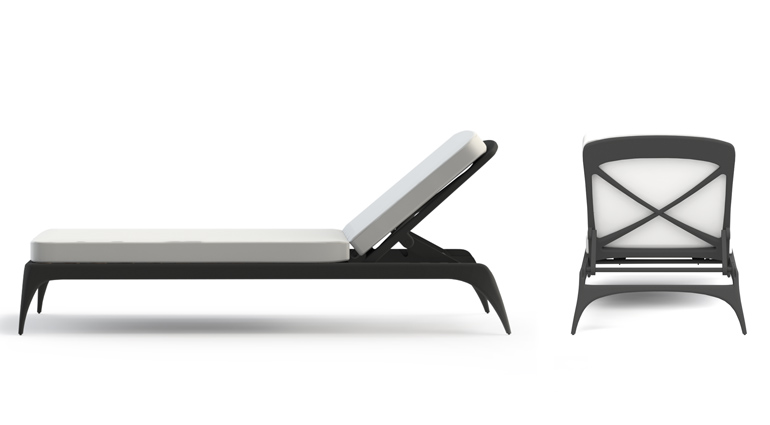
ID: What challenges do you often encounter when creating indoor/outdoor furnishings, and how does the collection address these?
JR: A major challenge in making any design is to recognize that it should far out last us—not only in durability, but in style and taste. So I try to create designs that have an aesthetic that does not necessarily fit any particular trend, but that celebrates the exploration of the process. Any product will start to show signs of age, picking up its own history unique to its use and part of the Flow collection, in particular, is to recognize the outdoors is a harsh environment and will continue to add to the journey of these pieces. They will not fail in structure or form, but the surface can take on the characteristics of a rock or stone, or more fittingly a vintage car that is discovered after years of exposure—there is a certain rugged beauty in the natural aging of things. The teak wood will silver and grey and the zinc patina will burnish and may even rub through in places, but this all adds to the allure of its durable solid core. Rather, like the legion of vintage Rolex collectors that scrabble over patinated watch faces, this aging cannot be imitated.
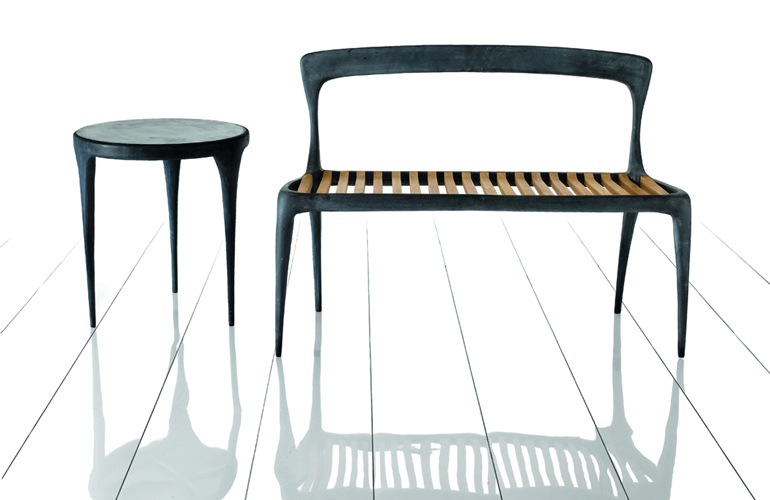
ID: How does this collection simplify the specification process for designers?
JR: The Flow collection smacks of solid durability, which is a big consideration for designers when it comes to the practical implications of use. The shapes and forms of these pieces are quite unique because many producers and designers would shy away from developing a fully cast aluminum frame like these due to the weight and cost. Indeed, by developing strong relations with my manufacturers, we have been able to achieve this range in the most cost effective way. The silhouette and open organic shapes of the product forms allow them to fit in with a natural environment, while the metallic nature of the material also enables it to work well in industrial settings, providing an interesting contrast of soft edges with hard architecture. There are so many potential atmospheres and environments that this furniture can help create, and it is my pleasure to maintain this collection along with the enthusiastic and vigorous backing of our very thoughtful and considered U.S. distributor Henry Hall, who is often reminding me of how he champions the Flow collection as a classic.
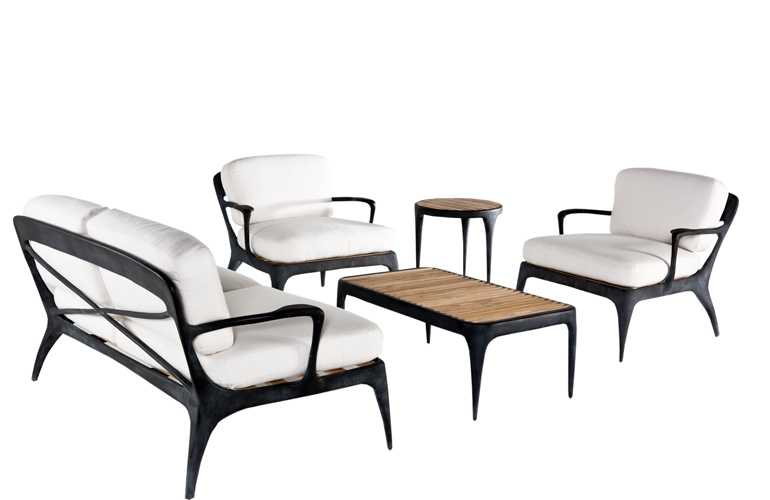